Meet SAPIN
"SAPIN SA has been PEFC certified since January 2004.
Since 1986, the company SAPIN is active in the purchase, sale and transport of timber, both in Belgium and abroad. Benoit Bauwens, a water and forestry engineer and member of the Fédération des experts forestiers de Wallonie, joined SAPIN SA in 1991. Among other things, he is responsible for the chain of custody and FSC and PEFC forestry certifications. The Royal Forestry Society of Belgium went to meet him.
Interview:
> Mr Bauwens, could you describe SAPIN SA for us?
SAPIN was set up in 1986 as a joint venture1 between various paper groups. SAPIN is active in the purchase (200,000 m3 per year either standing or roadside and 500,000 to 600,000 m³ equivalent in trade), sale and transport of wood as well as in maritime import. SAPIN delivers to paper mills, sawmills and pulp mills.
SAPPI2 has been the sole owner of SAPIN since the end of 2015. SAPIN is therefore a subsidiary of the SAPPI group.
> How has your company evolved since it was founded?
From the outset, SAPIN SA's vocation has been to supply paper mills with spruce wood for the production of mechanical pulp (as opposed to chemical pulp). We already had three sources of supply: sawmill chips, forestry operators and our own forestry department.
At the beginning of our activity, in the forest, there were what we commonly called "paper wood cuts", which were first, second and a few third thinnings. But technological developments in sawmilling changed all that. The primary processing industry started to saw small timbers. The "paper wood cuts" became small-diameter sawing cuts. SAPIN SA then focused more on softwood sawn timber to supply sawmills, from which it buys the chips for paper mills.
In 1994, SAPPI began to use poplar wood in addition to spruce, as it increased production speed and improved the whiteness of the paper.
> What is your parent company's strategy and how does it affect your business?
In 2019, SAPPI has invested around €145 million to produce a different type of pulp. This is a long-term investment with a continuous improvement process that will enable SAPPI to expand into new markets. The aim is to specialise in certain types of quality products. At present, we can supply SAPPI with most hardwoods. However, certain species such as chestnut, lime, acacia, etc. are excluded. At one time, SAPIN sold almost 2,000,000 equivalent cubic metres of wood a year, but in recent years we have negotiated and harvested between 700,000 and 800,000 cubic metres a year.
> What types of wood do you buy?
The main standing species are spruce, Douglas fir and larch. However, we also buy a lot of wood from the roadside or delivered to the factory, both hardwood and softwood.
> How much wood do you transport?
SAPIN has no warehouses. Harvested timber is delivered directly to the customer. The same applies to sawmill by-products, which are collected by us and then delivered to our customers.
> Where do you get your supplies?
SAPIN operates and trades within a 250 to 300 km radius of its head office. This includes northern France, Belgium, Luxembourg, the Netherlands and western Germany. We also import large volumes of sawn timber, paper and biomass from various European countries such as the United Kingdom, Ireland, Scandinavia and the Baltic States.
> What happens to these woods?
As mentioned above, SAPPI, our parent company, converts wood into luxury paper. Other products that SAPIN exploits are transformed into cardboard, MDF panels, OSB and, of course, sawn timber.
> How long has your company been PEFC certified?
SAPIN SA has been PEFC certified since January 2004.
> Why did you choose PEFC certification?
PEFC forestry certification has values in line with those of SAPIN. What's more, the paper market is a global market in which competition is fierce. For this reason, it is important for SAPIN to be certified so that its company does not lose business.
SAPPI, which is also FSC and PEFC certified.
> Is PEFC certification important to you?
When you want to have a long-term vision, you have to think in terms of resources - wood in our case - and ensure their sustainability. Certification systems offer these guarantees. It is therefore vital for a company like SAPIN that certification systems such as PEFC, FSC, SFI and other equivalents exist and guarantee the continuity and sustainability of our forests.
> Do you have a significant demand for PEFC-labelled wood?
At present, this demand comes mainly from papermakers and panel makers. But demand is also growing for sawn products. Added to this is the fact that sawmill by-products, i.e. wood chips, increasingly require labelling, prompting sawyers to start the certification process.
> What proportion of PEFC-labelled wood do you buy?
We currently buy and sell approximately 25 % of PEFC-certified wood. However, we have to take into account the fact that some of our suppliers have both FSC and PEFC certification and that we only use one at a time. Without this 'subtlety', the percentage of PEFC wood would be around 35 %.
> Are you finding enough certified wood?
The answer is clearly no. This sometimes forces us to import more wood. This is an aberration from an ecological and environmental point of view. If the required quantity of wood were available and certified, our imports could be greatly reduced.
Certification efforts should be made by owners, but they are not the only ones concerned. Merchants who do not commit to certification cannot sell wood from a certified forest. This is a loss for the downstream part of the industry.
> Do you ever pay a few extra euros for PEFC-certified wood or refuse to buy a batch that isn't certified?
This issue comes up regularly. Today, it is not a question of giving a "premium" for certified wood, but rather of penalising wood that is not certified.
Why this method? The answer is simple: competition for wood purchases is such that we always have to offer the best price, and a mark-up would not be economically viable.
> Are you buying in both private and public forests?
Yes, we don't make any difference at the time of purchase.
> In public forests, everything is practically PEFC? Isn't that enough for supplies?
Yes and no. In theory, yes, but the reality on the ground contradicts this statement, as many of our customers work with volume credit, making it physically impossible to separate stocks of certified and uncertified wood.
This means that SAPIN SA must carry out an annual risk analysis for wood from controlled sources, so that our customers can mix all our sources of supply. Clearly, if all incoming wood was certified, life would be a lot simpler...
> What would be the consequences for your company if you lost your PEFC label?
As described above, this is not an option.
> Since your company has been certified, have you noticed any changes in the market for labelled products?
Since 2004, it is clear that demand has increased, but this trend does not necessarily come from the end user, who makes his or her consumption choices not only on the basis of quality criteria or standards, but also on the basis of product price.
This increase in demand also reflects a desire on the part of the industrial sector to keep all market doors open.
> Do you think it's important for private owners to get certified?
Demand for wood has been exploding for several years now. Wood still enjoys a positive image. But today, this demand represents a risk to the survival and sustainability of the forest. We cannot ask the forest to be a major source of energy and the only building material. Forests can only provide what they produce. It would be absolutely counterproductive to tamper with this natural heritage.
One of the benefits of forest certification is that it guarantees manufacturers a source of supply for many years to come. Certification is therefore indirectly an incentive to invest and hire staff, and to get a country's economy moving.
Having your forest certified is also a way of showing that you're not just involved in financial speculation. It gives a very reasoned and reasonable image of the owners, and therefore gives confidence to our industrialists in the future.
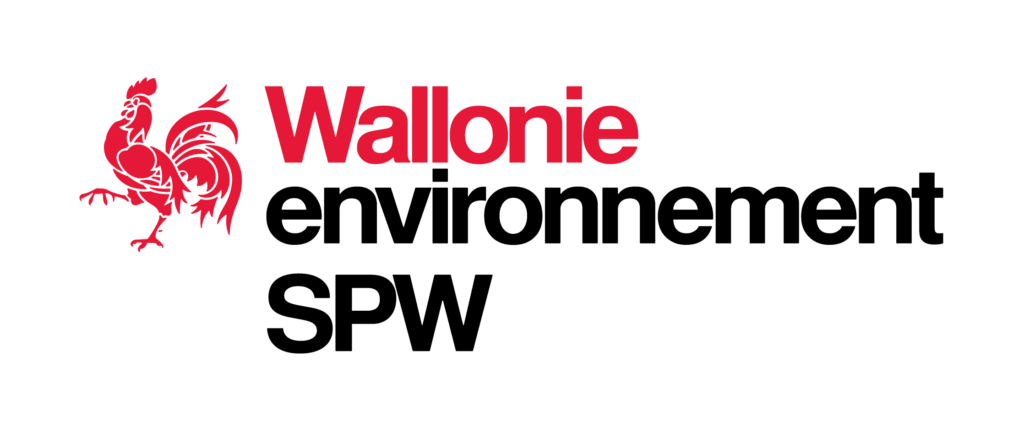
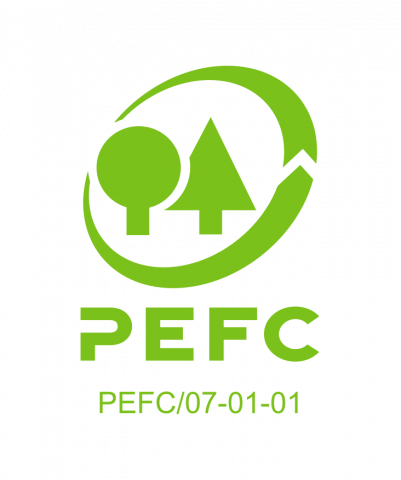
Photo: © Sapin SA
- A joint venture is an agreement between two or more companies who agree to pursue a specific goal together for a limited period of time. Source: Wikipedia
- SAPPI is a multinational company specialising in the production of DWP, pulpwood, release paper and biorefinery solutions for its direct and indirect customers. SAPPI Europe is Europe's leading producer of coated graphic paper as well as packaging and specialty papers. Source: https://www.sappi.com and
https://www.sapin.be/sappi/